SRNL Engineers Create Custom, Highly Efficient Additive Manufacturing System
A custom-built additive manufacturing system is now up and running at the Savannah River National Laboratory (SRNL). The lab’s Directed Energy Deposition (DED) system, which utilizes a powerful, class 4 laser, is designed to develop new alloys and parts for practical applications at speeds that significantly reduce the turnaround time compared to traditional manufacturing methods.
“If you create a model today, your component could be ready by tomorrow,” said Senior Advisory Scientist Guru Dinda. “You don’t need extra tools, dyes, or expensive machinery.”
“Some of the dyes and tooling that is required to make certain parts can take up to 15 to 18 months to set up and can be very expensive before you can begin manufacturing,” added Drew Snelling, research engineer. “This is a big factor when you have a need only for a low volume of parts.”
The DED system is comprised of a 3-kW diode laser enclosed in a Class 1 enclosure, an inert glovebox that houses a six-axis robot and two-axis positioner, four powder feeders, chiller, and a gas purifier. Each piece plays a critical role in ensuring the machine produces what the engineers are expecting.

The custom-built Directed Energy Deposition system uses the beam from a 3-kW diode laser as a heat source to produce materials. (Photo by Susanna King / SRNL)
While additive manufacturing is commonly known as 3D printing, Dinda says there is a slight difference in the way this machine produces parts. Normally in 3D printing, a thin layer of metal powder is laid out and then selectively melted by a focused heat source such as laser or electron beam, but the DED system has been customized to inject the metal powder into the melt pool from an outside powder feeder. Because it is an “open” machine, Dinda says they can change the feed rate of the four chosen metal powders at any given moment, quickly creating a unique material.
Once a sample is printed, the team ensures it is at 100% density, creating a need to check the material’s porosity or lack of fusion. This is when SRNL postdoc Raden Gustinvil gets to perform his work.
“We first perform optical microscopy – cutting the sample, sectioning, and mounting it to a block, and then grinding and polishing it to look at it through a microscope – primarily looking for defects and to see if it’s fully dense,” said Gustinvil.
The engineers also perform testing methods to identify impurities, observe grain structure, and determine mechanical properties.
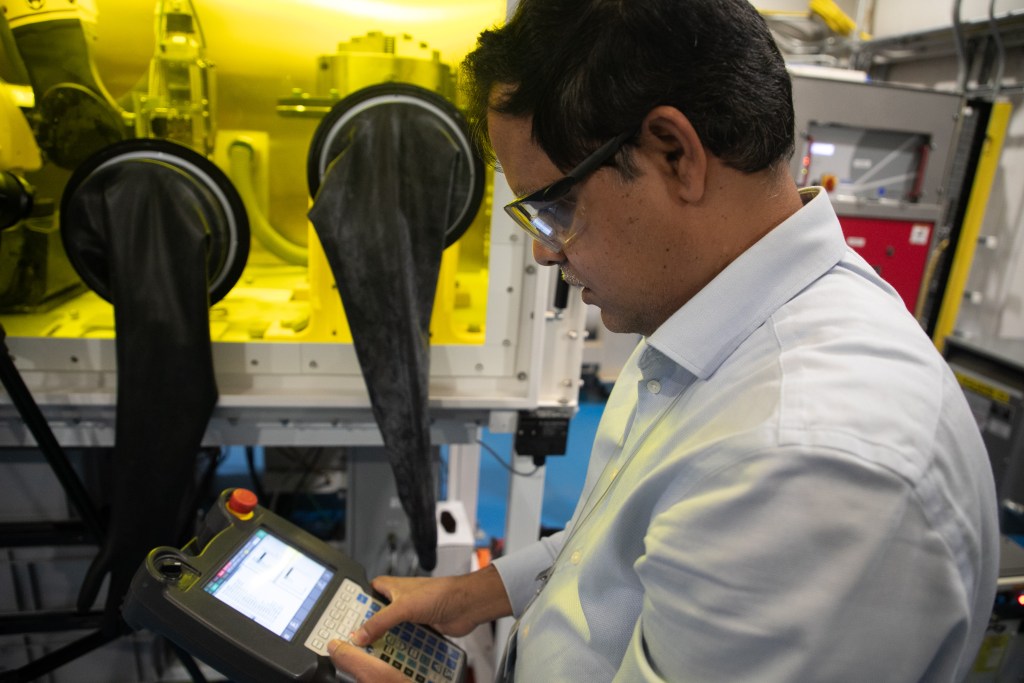
Senior Advisory Scientist Guru Dinda controls the feed rate of the DED system, and more, by entering parameters into the robot controller. (Photo by Susanna King / SRNL)
“We use our system to change the composition of what’s being printed and make it ‘friendly’ for additive manufacturing,” Dinda said.
The DED system is contributing to the development a new class of materials called high entropy alloys. Traditional manufacturing processes typically produce components with a single material. However, the DED system can produce multi-material components on-demand, including a specific material at a specific location.
“Any object that can’t be manufactured by a traditional technique can be printed here,” Dinda added.
Dinda, Snelling, and Gustinvil are looking forward to adding additional capabilities to the DED system, like sensors that can track what’s happening in real time while the machine is running, making it even smarter and more efficient.
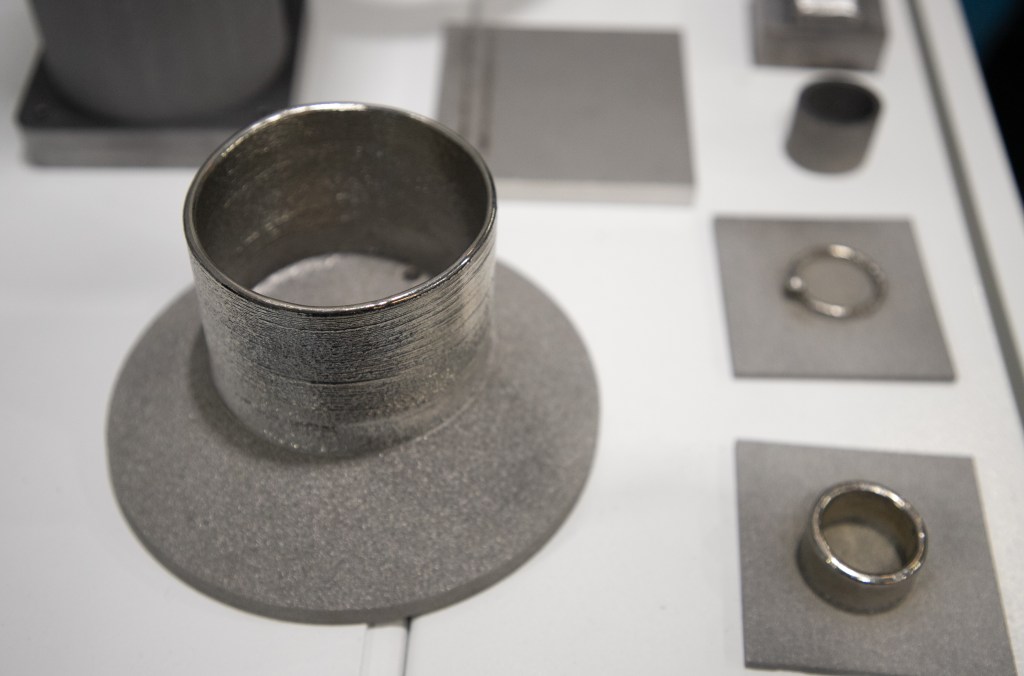
Sample printed materials from the Directed Energy Deposition system, which are used to test for impurities and to ensure the material is at 100% density. (Photo by Susanna King / SRNL)